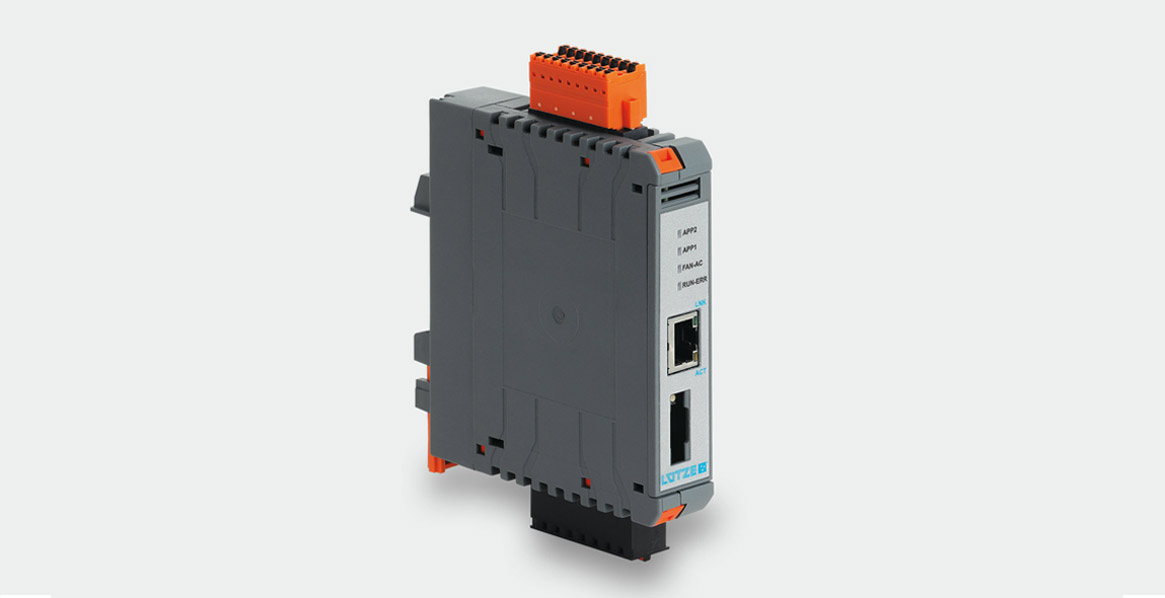
AirSTREAM Gets Smarter – Condition Monitoring in Control Cabinets with AirTEMP Controller and AirTEMP Monitor
With the AirTEMP 2.0 planning and calculation tool, control cabinets can be designed already thermally efficient and demand-driven.
The new AirTEMP Controller and AirTEMP Monitor solutions now add live-access condition monitoring. This type of temperature monitoring in control cabinets, offers plant and production line operators an innovative way to monitor, optimize, and significantly enhance operational efficiency.
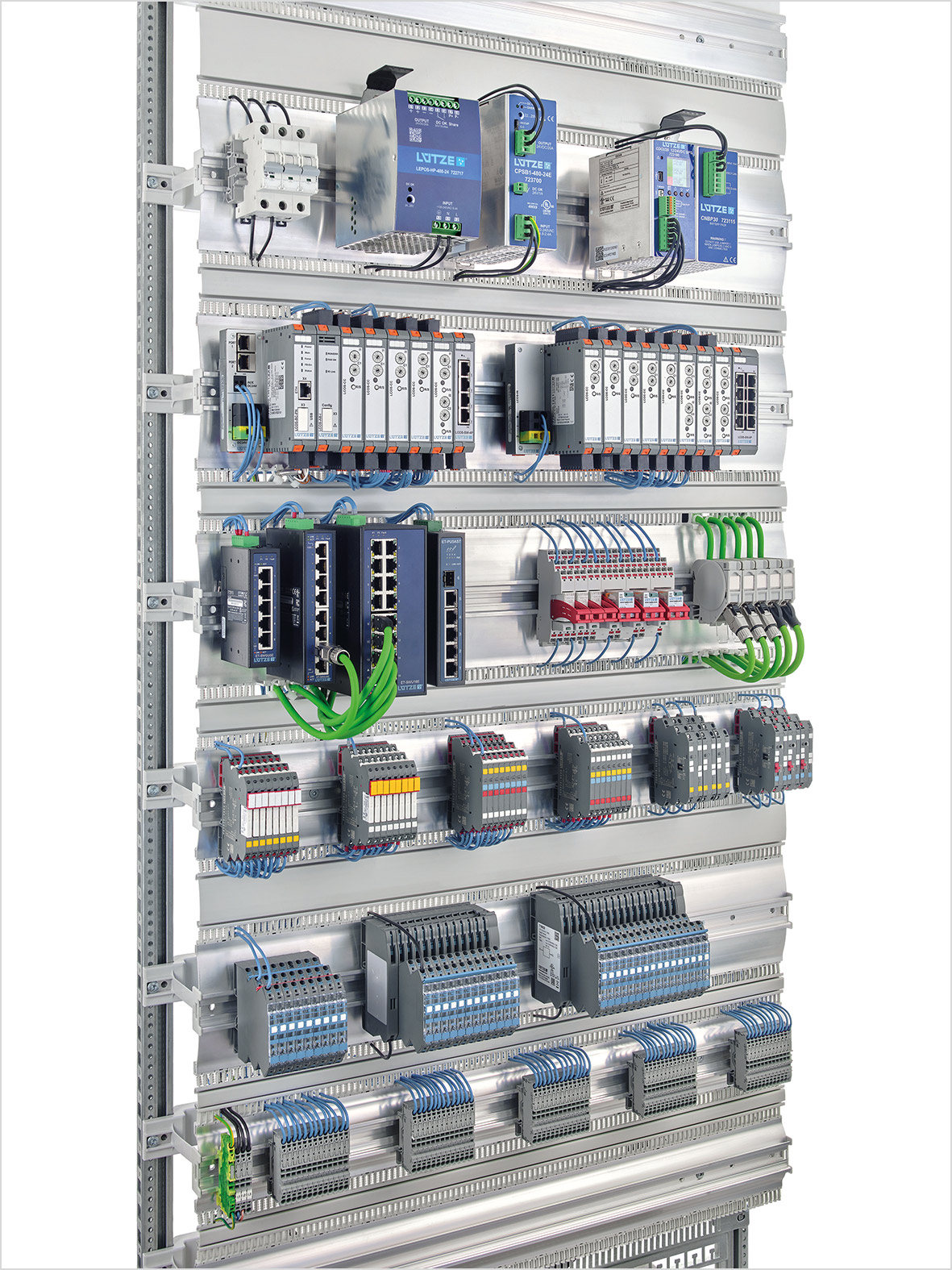
The continuously developed AirSTREAM system, consisting of an AirSTREAM wiring frame with integrated AirBLOWER fans, ensures targeted air circulation around the wiring frame inside the control cabinet. Now, with the new IoT solutions, it becomes intelligent. The goal of providing plant operators with increased operational reliability while keeping energy costs and CO₂ emissions in check, has been successfully implemented. Initial pilot projects tested in various customer processes have met customer expectations and now enable series release.
AirTEMP Controller
Measuring temperatures via a control unit to manage AirBLOWER fans is not a new concept. However, the ability to analyze, store, and monitor the collected data in real time makes the entire system smarter and helps improve efficiency in daily operations. The new AirTEMP Controller is an IoT-enabled control device. It has a relay output for controlling cooling units and an additional output for physical fault notifications. Of course, the functionality remains intact, allowing an output to control AirBLOWER fans to ensure temperature uniformity in one or multiple control cabinets. There are six PT 100 temperature sensors for temperature monitoring. The chosen number of sensors also makes it possible to use the system in cabinet series combinations. The recorded data is stored for a defined period and transmitted to the LÜTZE Cloud via the MQTT protocol. The AirTEMP Controller operates on 24V and can be easily retrofitted into existing cabinet systems.
AirTEMP Monitor
The cloud-based AirTEMP Monitor dashboard that is hosted in the LÜTZE-owned cloud, was developed to enable condition monitoring. The dashboard visualizes data using graphs, displaying temperature trends, fan bank operating cycles and possibly alarm signals. Through remote access, users can view and adjust parameters in real-time for each AirTEMP Controller. Custom temperature and alarm thresholds can be defined, and if necessary, active cooling systems can be triggered. Additionally, users can request regular reports via email, documenting the control cabinet status over a selected reporting period. The topic of predictive maintenance is ensured through the alarm function and was a key requirement in the development . Alarms can be sent via various communication protocols, ensuring fast response times and enhanced operational safety. This significantly reduces the risk of temperature-related failures and makes a sustainable contribution to the operational safety of control cabinets.
Demand-Based Cooling with AirBLOWER and Active Cooling
To further optimize demand-driven cooling, the system can activate additional cooling power when a preset threshold is exceeded via the relay output. LÜTZE has specialized in the thermal behavior of the AirSTREAM wiring system for years, always focusing on moving air efficiently with minimal energy consumption to protect components from overheating. If active cooling is also required, various smart solutions from market peers can be integrated. The goal is to ensure a sustainable cooling solution, even when combined with active cooling units. This results in a more efficient operating cycle, as less energy is required compared to running cooling units continuously. The primary aim is to first maximize the cooling potential of electrical components using energy-efficient methods. These efforts fall under the concept of demand-based cooling.
Outlook
The IoT solutions described, not only enable continuous monitoring and operational safety in ongoing operations, but also offer new approaches for the future. When new machine or plant generations are planned, the data collected from similar systems can be used for optimized design. Lütze is also working on a new digital solution for the planning of AirSTREAM wiring frames: a product configurator that generates 2D and 3D data, enabling easy project planning and seamless integration of the generated data into the respective CAD planning tool. This represents another step forward in optimizing control cabinet planning, as time is limited in daily operations, and the demand for efficiency-enhancing solutions is high. LÜTZE is committed to the collaborative development of innovative solutions for sustainable control cabinet planning and operation.
Authors:
Michael Bautz, Product Manager Cabinet, Friedrich Lütze GmbH
Daniel Haag, M.Sc., (University of Stuttgart, Institute for Building Energy, Thermal Engineering and Energy Storage)