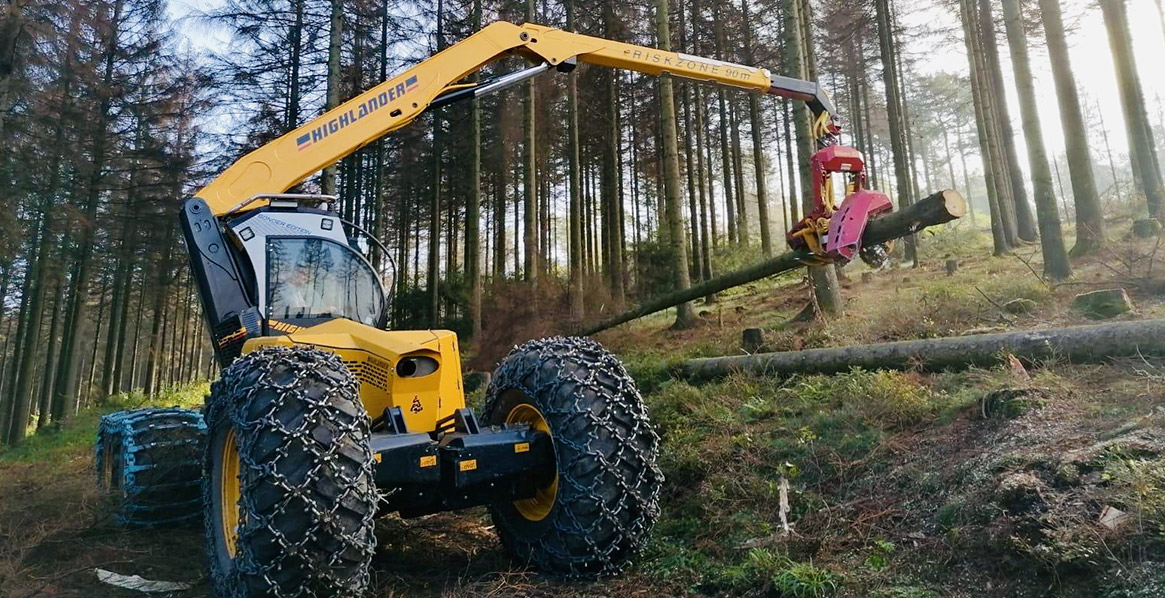
Tearing down trees - correct connectivity when harvesting wood
- Product range:
- Connectivity
The six-wheel spiderweb vehicle works on steep mountain slopes. Thanks to the 6x6 four-wheel drive and synchronous driving and stepped movements, the forestry workers can maneuver it very flexibly, all from from the driver's cab. This wood harvesting machine has proven its worth in the most challenging forests.
In addition to the wheel harvesters of the 'Highlander' series, Konrad Forsttechnik GmbH in Kärnten also produces various wood harvesting machines on wheels or caterpillar tracks, as well as cable cranes for inaccessible steep slopes. Here, the suspended harvesting aggregate is directed to the work site by remote control.
Faster than ten forestry workers
The actual tree harvesting is carried out by the multifunctional aggregate 'Woody'. Hanging from the crane arm, it carries out three tasks: felling trees, lopping off branches and sorting. From inside the cabin, the forestry worker first places the aggregate grabber around the tree trunk, extends the chainsaw and cuts it. Then the grabber turns the trunk quickly into a horizontal position and pushes it between two tooth-edged endless rotators that lop off the branches very rapidly. A feeder unit saws the trunk pieces into the required length. It only takes minutes for the grabber to stack these cleanly before moving onto the next tree.
Even at -30°C, you can shout 'Timber!'
One can only imagine how complex the cable tree design needs to be to control everything: the grabbers, brackets, rollers, rotators and pressure sensors, as well as the top saw and chopsaw, including the chain adjuster and the wing blades. And everything needs to function perfectly in every climate: be it hot or cold, humid or in the greatly varying ambient temperatures where the machines are used, for instance -25°C to +40°C, because the harvesters work from Norway to Spain. This special piece of equipment from Oberpreitenegg is even used in Asian and South American countries.
Only excellent quality can withstand these extreme demands
And the amount of trouble there would be, if a machine would fail in a remote forest, not to mention the expense of the downtime. Forestry workers depend heavily on absolute reliability - just like the manufacturer Konrad depends on the quality of its suppliers. As far as Cable and Connectivity is concerned, Konrad has maintained a partnership with LÜTZE for approximately 15 years. Whilst the initial focus was on the various cable assemblies, over the years the company started to demand even more complex cable trees, some with more than 30 wires and 2-pin German plugs or rectangular, high-pole hybrid connectors for the automobile sector - you can' see the woods for the cables.
Excellent solution for LÜTZE SUPERFLEX interconnector
We currently supply nine cable tree types. One very difficult task: a cable tree that needs to be connected using two parts. On the one side, the LÜTZE SUPERFLEX® PLUS N PUR C-train-suitable cable, and on the other, the flexible, temperature-resistant single-core cables of another cable bundle – and both need to have no air inclusions and be absolutely humid-proof after the wires have been soldered. LÜTZE developed solutions without silicon-filled shrink hoses and presented the samples. They selected a cable manager that works with an extra jacket and PUR adhesive. An idea that goes above and beyond the specifications, fulfills the purpose even more reliably and also looks very neat.
Own cable competence centre
Konrad continuously optimizes its products and develops new models. Accordingly, modified or completely customized solutions are required. And LÜTZE is able to deliver. Thanks to the deliberate proximity to its customers, it can react flexibly and quickly. For instance, there was a request for a specific cable with a very wear-resistant and smooth-running outer jacket that had an outer diameter that was as small as possible, maximum 11.0 mm. LÜTZE redesigned the cable so that it slides more easily and only measures 8.0 mm. After the first 500 m sample was delivered, several thousand meters were ordered successively. Then Konrad required the outer diameter to be changed to 9.0 mm to make it more durable to mechanical stress.
The LÜTZE Connectivity Competence Centre in Czech Republic is always involved in these customized solutions: All activities of the LÜTZE Group in the cable assembly field have been bundled here since the middle of 2019. The resourceful colleagues in the center like to apply their wealth of know-how. And they do everything they can to rise to any challenge and come up with a solution that is better than expected.
Author: Arnela Naunovic (engineer), Product Market Manager LÜTZE Austria
Picture credit cover: Konrad Forsttechnik