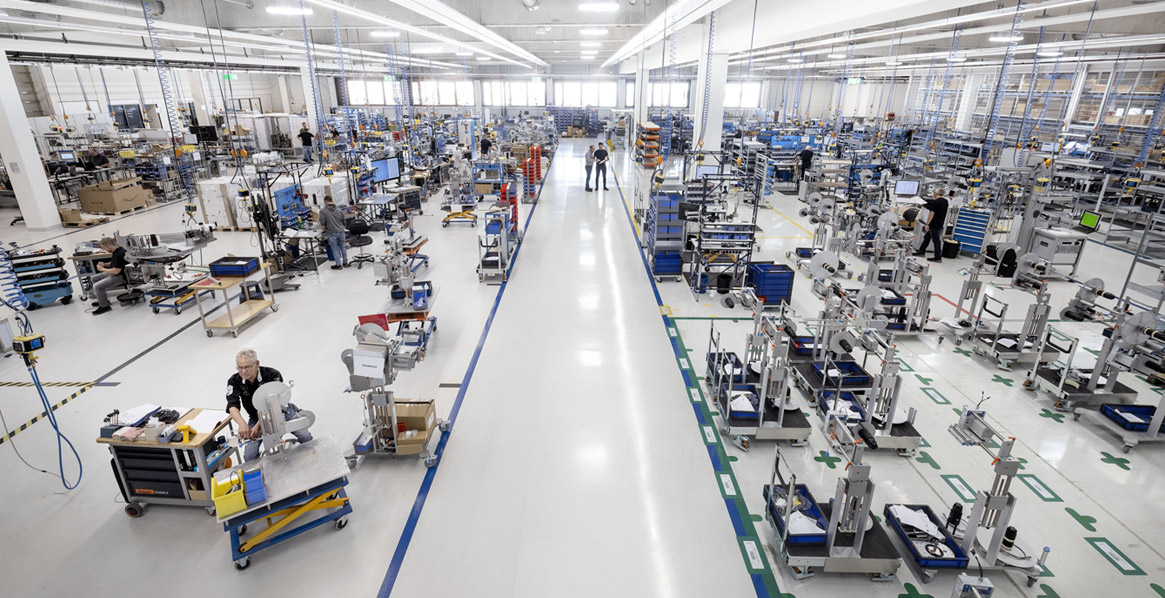
HERMA wires labeling machines without ducts
- Product range:
- Cabinet
HERMA is adhered to food and cosmetic packaging, clothing labels, book spines, medicine ampoules and thousands of other everyday objects; likewise, to practically all semi-finished products, from automobiles to electronics. Without adhesive labels and the printed information, logistics and order picking processes would come to a standstill. HERMA can supply the matching label types for any feasible application - it is like the glue that keeps the world of goods together.
From a small inventor workshop to a market leader
The company started in 1906 as the 'Heinrich Hermanns Stuttgarter Druckbetrieb' that produced embossed labels and tags for the growing number of goods that were being manufactured by industrial operations at that time. The company's steady flow of new ideas, including adhesive rolls or 'rapid moisturizers', some of which were produced on machines HERMA had developed, drove its growth. In the 1930s, the company landed a huge success with their photo corner stickers that we all know from our old family photo albums. The 1950s saw the boom of supermarkets – and everyone needed the little self-adhesive price labels by HERMA. The company used its machine construction expertise to develop 'labelers'. Since then, HERMA has kept on coming up with new product and production solutions needed by the market. Success has stuck to HERMA for many decades, a fact that was underscored in 2019 with the construction of the brand new facility in Filderstadt near Stuttgart, which became Europe's most modern labeling machine production plant.
Goodbye mounting board
When the machine portfolio was overhauled, the control cabinets of all five machine types were switched to the LÜTZE wiring frame AirSTREAM. Previously, the predecessor system LSC B had been used. The head of the electrical assembly team, Marc Freund, is very excited about this intelligent wiring solution: "Anyone who is familiar with the AirSTREAM knows how superior it is compared to mounting boards." The winning arguments are the significant space savings and more efficient use of the available space. How can this extremely compact system reduce the size of control cabinets by up to 30 percent? It's simple: cable ducts are no longer required because the wiring level is already integrated into the frame. This leads to other benefits compared to conventional designs, for instance, the cabinets only need to be wired from the front, which is a much simpler process. The separated wiring and component levels allow the electronic parts to be equalized when installed, especially those with high thermal outputs. The almost freely circulating air removes the heat, which in turn reduces the risk of hot spots and therefore heat stress, as well as minimizing part failure. Marc Freund also highlights the fact that the LÜTZE frame is delivered completely assembled. "Instead of working with a mounting board, the finished wiring frame only needs to be configured – this saves a lot of time." Even the subsequent replacement of modules or the addition of new modules is much quicker with the AirSTREAM. His summary: "We never want to return to mounting boards".
Brand new Compact version in use
The head of the electrical assembly team greatly appreciated the intensive on-site support offered by LÜTZE sales team during the machine switchover phase. He is so satisfied that he has recommended the manufacturer to other departments, for example, cable assemblies are currently under discussion. In the test, the LOCC-Box for current control is installed in HERMA's next world innovation: the InNo-Liner System processes labels without carrier material. The initially non-sticky adhesion material only activates by means of micro atomization when dispensed - in the future, this will save many tonnes of carrier material every year. This is a sustainable approach that LÜTZE likes to support: the new Compact version of the AirSTREAM, the latest innovation of the AirSTREAM wiring system, is fitted into the machine's control cabinet. Like the standard version, the AirSTREAM Compact can cut cooling energy by up to 23% thanks to the homogenous climate in the control cabinet. This is, in part, also due to the very favorable flow properties of the proven rail profiles of the standard program. In general, the AirSTREAM Compact stands out thanks to its very high rigidity. Now, for the first time, space-saving and flexible wiring is available for small control cabinets, in particular narrow or special cabinets fitted into other systems. The user can select from the wide range of accessories for the recently expanded AirSTREAM program.
Author: Jessica Stoll, sales engineer at Friedrich Lütze GmbH