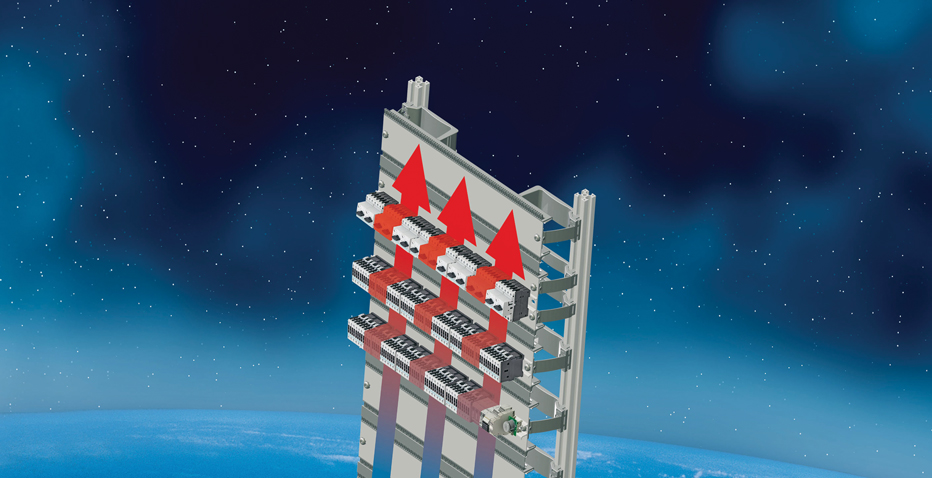
Cabinet climate control for the automotive Industry
- Product range:
- Cabinet
The automation specialist Friedrich Lütze GmbH & Co. KG has committed itself to energy and cost-efficient air conditioning in automation technology (Project InnoCat 4.2.1) within the Alliance for Innovation "Green Carbody Technologies".
The research interest focuses on the reduction of energy expenditure needed for the cooling of control cabinets. The backgrounds to the LSC wiring system and Alliance for Innovation will be presented by LÜTZE and the project partners at the Hannover Fair 2011.
How important is the air conditioning of control cabinets for resource and energy efficient vehicle production? This is one of the many questions that the Volkswagen AG would like to answer within the Alliance for Innovation "Green Carbody Technologies". For that reason, the Alliance for Innovation was set up in 2009 together with the FRAUNHOFER-Institute for Machine Tools and Forming Technology (IWU) in Chemnitz. The research project is sponsored by the Federal Ministry of Education and Research. 60 companies in Germany in the joint project, including 20 companies in subproject 4, have joined together in the meantime to establish the Alliance for Innovation. A period of three years has been scheduled for the project.
Perfect Climate in the Control Cabinet?
Within the automotive industry in particular we see that a significant part of energy must be expended for the air conditioning of control cabinets in addition to the primary energy requirement for production. Cooling by means of ventilation and cooling plants is necessary due to the heat loss of the integrated electrical appliances. Owing to the distribution of heat in the control cabinet that is often very heterogeneous, the so-called "localised hot pocket", the cooling is additionally determined by the highest temperature ranges in the control cabinet.
Thus, apart from LÜTZE another 20 participating partners such as Volkswagen AG, Audi AG, Rittal GmbH & Co. KG, Phoenix Contact Deutschland GmbH and PTKA (Project sponsor Karlsruhe in the Institute for Technology) have set themselves the goal of lowering the energy requirement for control cabinet cooling by up to 15% and reducing the space required for installing control cabinets by up to 30%. Important stages for this are the optimisation of wiring systems for producing a laminar (turbulence-free) airstream in the control cabinet and the avoidance of heat pockets.
Manufacturers of cooling appliances have the additional task of reducing the energy requirement. The optimisation of cooling appliances with the aid of modular, adaptive control and regulation systems plays a decisive role here. A positive side effect: By reducing the heat loss in the cabinet the lifetime and thus the operating time of the electrical components in the control cabinet is increased.
What role does the control cabinet play?
Experiences with LÜTZE LSC control cabinet systems over recent years show that intelligent concepts for the air circulation in the control cabinet reduce the cooling requirements quite significantly and can thereby minimise the heat stress for components. LÜTZE has developed a clever solution for the "heat problem" in control cabinets with its LSC-wiring system: The LÜTZE system utilises an additional level in the depths of the control cabinet. The wiring is moved from its traditional position between the switching devices to the rear. This firstly saves space in the control cabinet, and secondly, allows improved air circulation between the appliances. As a result, the heat transfer to the air is greatly improved. In concrete terms: "Heat pockets" are avoided to a large extent. Studies in recent years show, for instance, that heat dissipation with the LSC-wiring system is up to 15% better than with comparable conventional control cabinets.
The test setup in practice and associated modelling
Within the framework of the research project, the thermal behaviour is currently being recorded and analysed at the Volkswagen AG by means of 48 sensors in the control cabinet in-situ – i.e. under the conditions that exist in practice. In parallel, the thermal behaviour is replicated in the control cabinet ex situ – i.e. under laboratory conditions. With the help of the variation of different changing parameters a model is to be simulated for temperature and flow field changes. The aim of this simulation is to point out and quantify measures and parameters for increasing energy efficiency.
LÜTZE with an optimistic vision of the future
The head of LÜTZE, Udo Lütze, a member of the steering committee of the Green Carbody Alliance for Innovation is certain that the basic research will pay off in the long-term: "The competitiveness of the German automotive industry and its suppliers depends very significantly on how we manage to develop practical results here. The results we jointly develop today are our competitive advantages for the future. And it's for this very reason that the collaboration between suppliers, automotive manufacturers and science is more than gainful“.