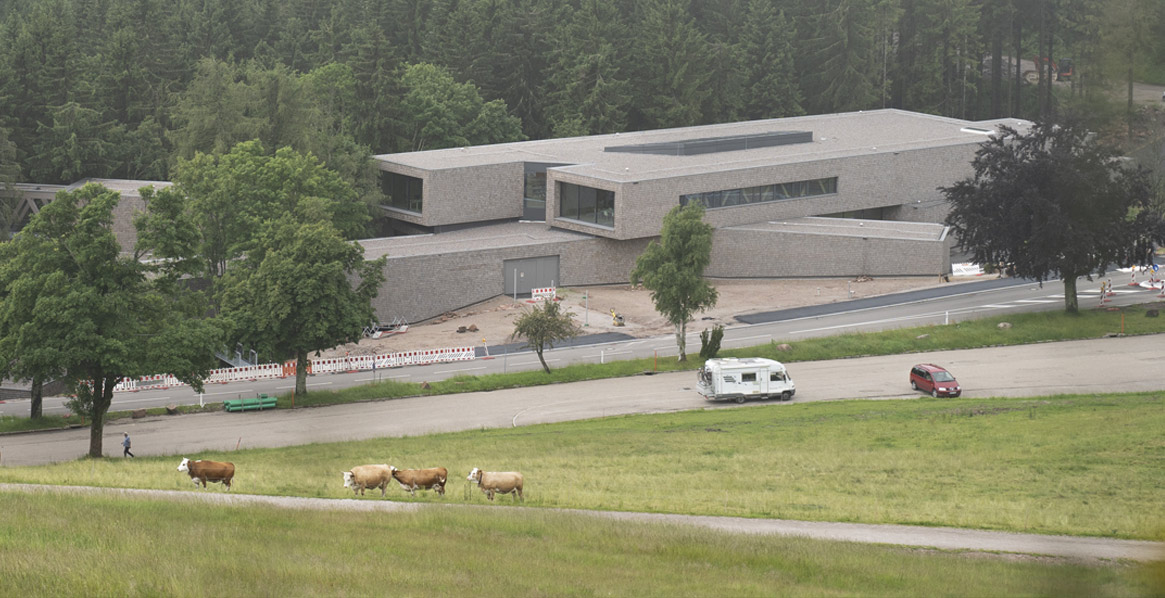
Green balance sheet for building automation
- Product range:
- Cabinet
Out in the rugged countryside and the wild beauty of the Northern Black Forest region, there is a construction with an extremely oblique geometry: eight long building blocks that are arranged like crisscrossing tree trunks. The design aims to replicate the typical forest of the national park - namely, untamed nature.
The Ruhestein national park centre is located in the middle of a 10,000 hectare virgin forest. Visitors can experience interactive exhibitions across several floors, covering 3200 square meters. on biodiversity, habitats and the creation of the wilderness. A cinema, cafe and a shop are almost standard today – but not a skywalk and a 34 meter observation tower with a panoramic view of the 120 year old forest. It is surrounded by hiking and cycling paths, cross-country ski trails and ranger guides.
Built along sustainability principles
Created based on state-of-the-art timber construction technology, the complex structure of the building was a huge challenge for the architects and structural engineers: for instance, the building blocks needed to be integrated into the existing trees, removing as few trees as possible; some blocks protrude freely into the forest. A few building frames are actually circled around individual trees. The building envelope has thermal protection like a passive house; the heat and warm water are generated by two pellet heaters - of course - and there is also a buffer store. The air is conditioned via decentral, mechanical ventilation systems. Cooling in summer is achieved using two underground extinguishing water cisterns: the circulating water absorbs heat from the exhibition area, flows through the warm water thermal pump in the kitchen and back to the cisterns via an earth collector field.
The control cabinet is very small
The building automation system with its measuring and control instruments is therefore highly complex. It was designed by Christian Bachhäubl e.K. from Baiersbronn, a regional specialist for heating and electrical equipment, and building automation systems. As it has done many times in the past, the company is cooperating again with the company Jürgen Tapper GmbH from Höheischweiler on the MSR technology for this key project. This expert for individual controllers and control systems, wires all control cabinets for Bachhäubl. One reason for this is that only the AirSTREAM wiring frames by LÜTZE are used. As an 'enthusiastic user' of this concept for many years, because it is 'much superior to conventional mounting frames', Michael Wagner (CEO of Tapper GmbH) fully agrees with Christian Bachhäubl. The national park centre profits from the fact that the control cabinets are up to 30 percent smaller, thanks to the AirSTREAM System, which means that the project partners were able to show their theoretical prowess right from the outset. In practice, it was possible to save an entire field using the modular cabinets.
Ecological footprint in a small shoe size
Another advantage of the AirSTREAM frame is its clever cooling concept: thanks to the duct-free design, the freely circulating air flow discharges thermal losses, which in turn homogenizes the climate in the control cabinet. Thanks to the AirBLOWER fans combined with AirBLADE baffle elements, the air flow can be specifically directed, for instance toward potential hotspots. This reduces the risk of thermally-induced component failures – and therefore, also removes the need for cooling energy and the associated CO2 emissions. Compared to industrial applications, the output fitted in the cabinets is lower, but this sustainability aspect is of great advantage to the climate – after all, everything counts! How much does a climate-friendly control cabinet cooling system contribute to the ecological footprint? A practical study came to an astonishing result. Let's imagine we are walking from the Black Forest into an industrial production facility.
76 % savings potential for CO2
The level of potential CO2 savings in the control cabinet is often underestimated. For instance, if we take a look at an industrial production facility in the automobile sector: here, LÜTZE works with several German manufacturers, with the AirSREAM wiring system as an industry standard, because these factories have recognized that the cooling energy and emission reductions in the control cabinets play a role in the CO2 footprint of an industrial product.
This can accumulate to a considerable figure as shown in the following example: the starting point were two typical control cabinet combinations, both with the duct-free AirSTREAM wiring system. One with an active cooling system, the second with just seasonal cooling in the summer months plus the AirBLOWER fan system. . The result: the CO2 emissions were reduced from 204 kg annually to 48 kg. If this savings potential of 76 percent is scaled to an entire production facility, 200 of these control cabinets would achieve savings of 85,000 kWh and 31 t CO2. This was calculated with the German power mix of 2020 with some fossil fuels. This practical case study was conducted by Friedrich Lütze GmbH and the University of Stuttgart Institute for Building Energy (IGTE). Both have been cooperating for many years on needs-based and environmentally-friendly cooling concepts for control cabinets. The extensive study is available via the LÜTZE homepage in the Topic section.
Authors:
Bernd Hütter, Product Market Manager, Friedrich Lütze GmbH
Michael Mölich, Sales Engineer, Friedrich Lütze GmbH