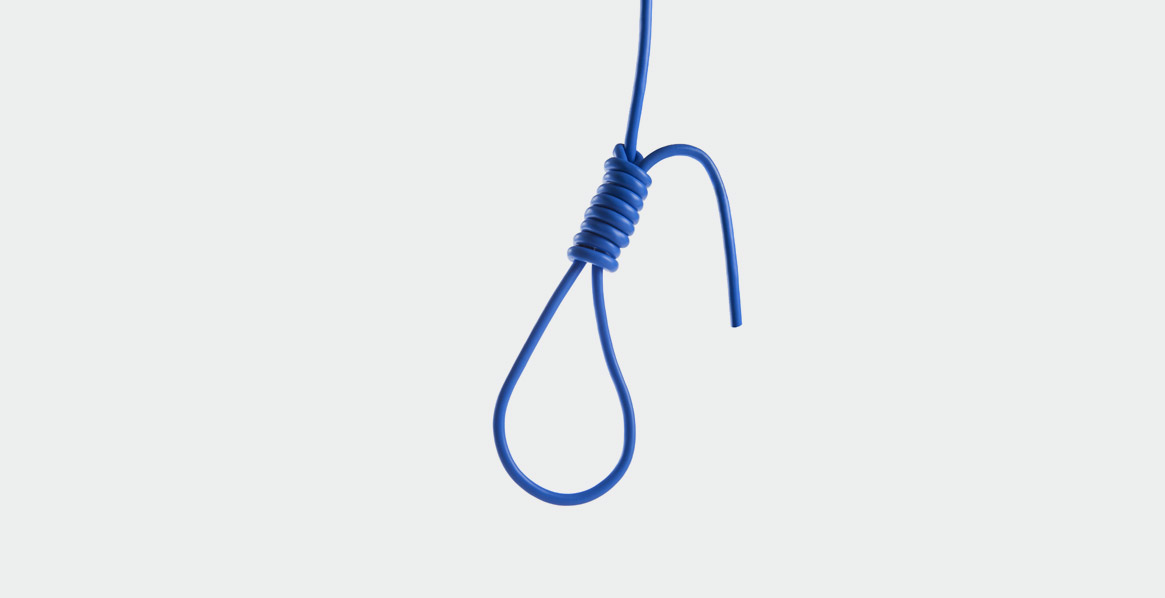
Gegen den Leitungstod
Oft wird der Auswahl der passenden Motorversorgungsleitung viel zu wenig Aufmerksamkeit geschenkt. Das Problem: Der Frequenzumrichter erzeugt elektrische Phänomene, welche die Leitung im späteren Betrieb sehr stark elektrisch und mechanisch belasten können. Kurzum: Der frühe Leitungstod ist vorprogrammiert. Welche Faktoren sind also bei der Auswahl einer Motorversorgungsleitung zu beachten?
Frequenzumrichter müssen Motoren für bewegliche Maschinenbestandteile untereinander genau steuern und deren Geschwindigkeiten exakt regeln. Besonders wichtig ist dabei eine effiziente Leistungsauslastung. Während früher Asynchronmaschinen mittels Schützsteuerung von 0 auf 100 Prozent ihrer Leistung geschaltet wurden, kann heute durch ein effizientes Energiemanagement der Verbrauch genau abgestimmt werden.
Leitungen, die Motoren über Frequenzumrichter steuern, unterliegen einem besonders hohen elektrischen und mechanischen Stress. Das ist der Grund, weshalb Steuerleitungen mit konventioneller Isolationsdicke und der daraus resultierenden Nennspannung U0/U=300V/500V, für Applikationen dieser Art nicht mehr ausreichend sind. Die richtige Motorleitung überzeugt mit einem langen Lebenszyklus und spart die Energie ein, die für die Bewegungsenergie am Motorende benötigt wird. Sie schirmt Störfrequenzen von außen und innen ab und reduziert die allgemeine Temperatur in Kabelkanälen. Symmetrische Motorleitungen können sogar helfen, die Lebensdauer der Kugellager im Motor zu verlängern.
Legt man auf die Leitungsdefinition für Servo- und Motorapplikationen nicht genügend Wert, muss man sich mit folgenden Stressfaktoren auseinandersetzen:
- hoher Ladestrom, mehr Wärmeenergie,
- reflektierende Wellen,
- Koronaeffekt.
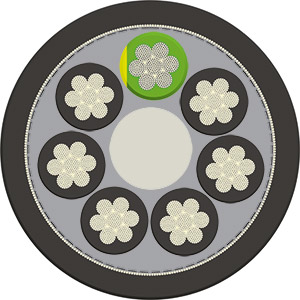
Low-Capacity Motorversorgungsleitung mit symmetrischem Aufbau und gedritteltem Schutzleiter
Stressfaktor 1: Hoher Ladestrom, hohe Wärmeenergie
Durch den binären, hochfrequenten Schaltprozess und den damit verbundenen schnellen Spannungsanstieg an der Ausgangsseite des Frequenzumrichters, spielt die Länge der Motorleitung eine wichtige Rolle. Der Raum und das Material (hauptsächlich die Isolation) zwischen den Leistungsadern verhalten sich prinzipiell wie ein Kondensator. So kann sich selbst bei Isolationsmaterialen mit niedriger Kapazität ein Ladestrom von 0,6 Ampere pro Meter ergeben. Bei einer 25 Meter langen Leitung ergäbe dies bereits 15 Ampere Ladestrom, mit der die Leitung erst geladen werden muss, bevor der Motor Leistung aufnehmen kann. Abgeschirmte Leitungen sind davon besonders betroffen, da zwischen Adern und Schirm zusätzlich kapazitive Energie anliegt.
Ein weiterer Energieverlust wird deutlich, wenn man die Temperatur im Leistungsteil der Kabelkanäle prüft. Der schnelle Anstieg der Polarität des Frequenzumrichtersignals, in Verbindung mit dem Ladestrom der Leitung, erzeugt eine hohe Wärmeenergie. Die Wärmeentwicklung ist also in erster Linie frequenzabhängig. Hauptausschlaggebend ist hier die Dielektrizitätskonstante (Permittivität) des eingesetzten Isolationsmaterials. Lütze setzt darum bei seinen Low-Capacity-Motorleitungen in erster Linie auf zwei Materialkomponenten: XLPE und PP. XLPE bieten als Isolationsmaterial eine deutlich niedrigere Kapazität als PVC. Damit verringert sich das Aufladen der Leitung und die Verlustleistung durch Wärmeenergie.
Stressfaktor 2: Reflektierende Wellen
In der Regel ist die Impedanz des Motors höher als die der angeschlossenen Leitung. Dieser Unterschied kann eine sogenannte reflektierende Welle erzeugen, die aus zwei sich überlagernden Spannungswellen besteht. Eine Spannungswelle, verursacht durch den Anstieg des Stroms Richtung Motor ausgehend vom Frequenzumrichter und eine reflektierende Spannungswelle von Richtung des Motors kommend (ein Rückstau des Stroms durch den unterschiedlichen Wechselstromwiderstand) überlagern sich. Dies kann die Spannungshöhe in kurzen Momenten auf das doppelte erhöhen – und damit die Isolation stark beanspruchen. Bei langfristigen Ermüdungserscheinungen der Isolation kann diese Belastung zu einem Kurzschluss innerhalb der Leitung führen.
Die Länge der Leitung ist hier ebenso ausschlaggebend für das Auftreten dieses Phänomens wie auch die Isolation. Je näher der Impedanzwert der Leitung an dem des Motors liegt, umso geringer ist die Wahrscheinlichkeit für das Auftreten einer reflektierenden Welle. Lütze setzt darum für seine Low-Capacity Motorversorgungsleitungen auf das niederkapazitive Isolationsmaterial XLPE. So wird das Delta zwischen Motoren- und Leitungsimpedanz reduziert. Zudem sind durch das geringere Delta längere Leitungslängen möglich.
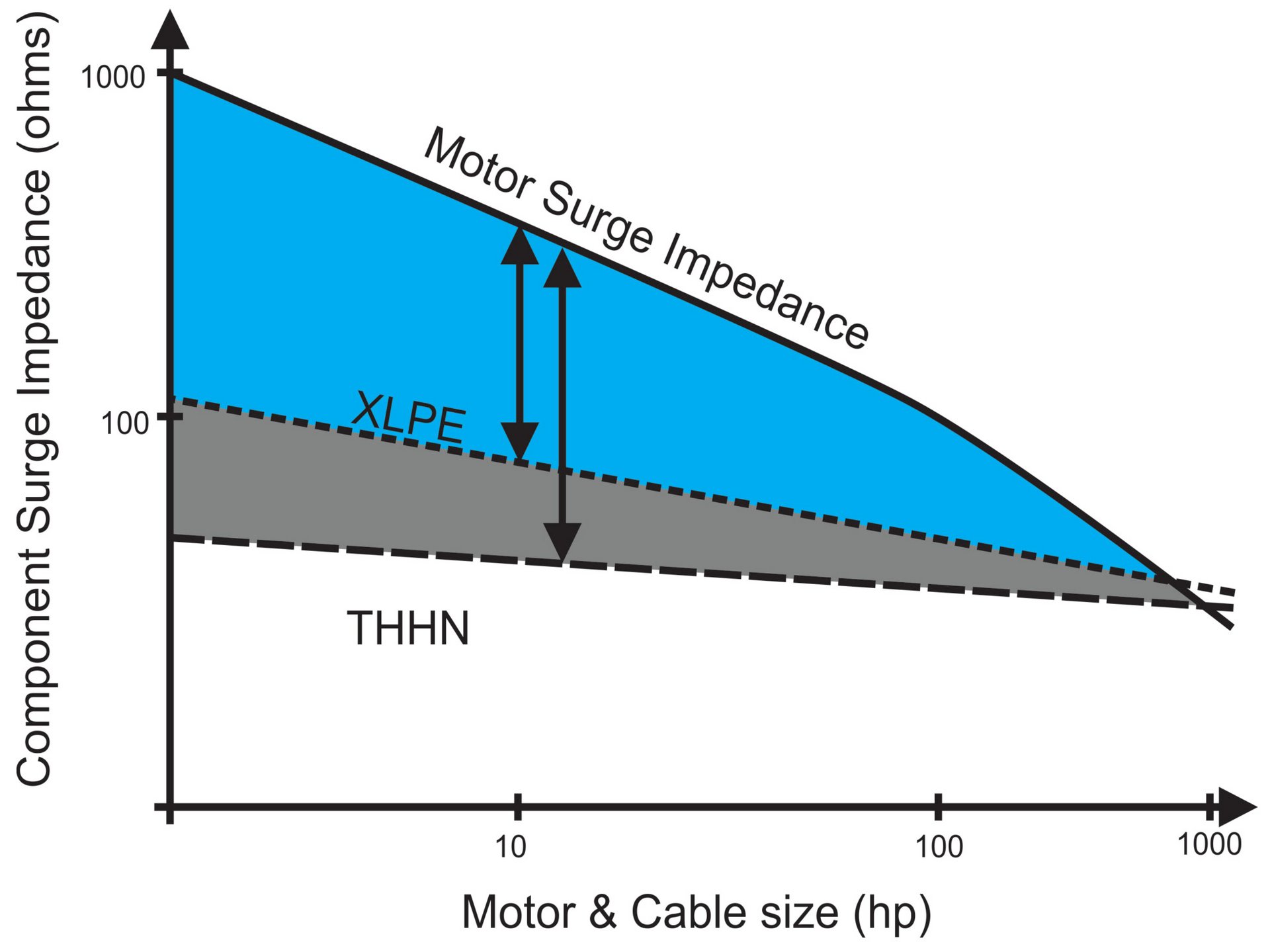
Ein niederkapazitives Isolationsmaterial reduziert das Delta zwischen Motoren- und Leitungsimpedanz
Stressfaktor 3: Der Koronaeffekt
Hohe Spannungen können ein elektrisches Feld erzeugen, welches die Luft zwischen Mantel und der Isolation ionisieren kann. Erreicht diese Spannung eine gewisse Höhe (elektrische Feldstärke), wird eine Koronaentladung hervorgerufen. Die Höhe wird durch die Koronaanfangsspannung definiert. Koronaentladungen erzeugen neben ultraviolettem Licht Ozon, welches die Isolation schwächt. Wird dieser Prozess nicht unterbunden, altert die Isolation schneller und weitere Gase werden freigesetzt, welche die Leitung noch weiter schwächen. Dieser Prozess beschleunigt sich zusehends, bis die Leitung schlussendlich versagt. XLPE als Isolationsmaterial zeigt auch in diesem Fall einen positiven Effekt, da es im Vergleich zu PVC eine wesentlich höhere Koronaanfangsspannung und höhere Spannungsfestigkeit besitzt. Darüber hinaus kann über die dickere Isolationsschicht die Koronaanfangsspannung erhöht werden.
Motorleitungen mit symmetrischem Aufbau
Insbesondere bei größeren Motoren können Spannungen in die Motorwelle oder das Motorengehäuse induziert werden. Diese Spannungen entladen sich über die Lager des Motors und beschleunigen den Abnutzungsprozess. Abhilfe schafft hier ein symmetrischer Aufbau des Schutzleiters durch die gleichmäßige Verteilung und Aufteilung in drei magnetische Felder.
Motorleitungen mit symmetrischem Aufbau erzeugen ein gleichmäßigeres Magnetfeld um die Leitung, so wird die Induktionswahrscheinlichkeit reduziert, die Lager der Motoren werden weniger belastet.